As Bill McInnis from Reebok Future puts it, “shoes are expensive because molds are expensive.” So, what would happen if you removed molds from the equation?
Reebok’s Liquid Factory has created a new way to build shoes from the sole up. Using 3D drawing, sneakers are drawn with a special plastic developed specifically for this process by BASF. The process is similar to 3D printing, using much of the same technology. However, 3D drawing is built around using liquid plastics and rubbers, rather than the stiffer plastics used in 3D printers.
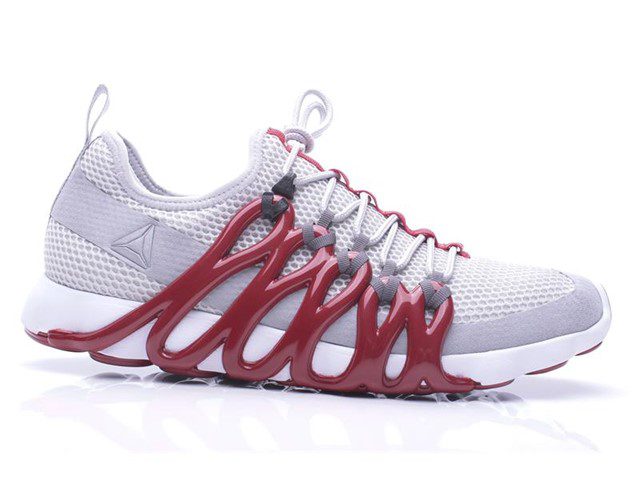
THE SCIENCE
McInnis is a former NASA engineer. His experience with space-age technology-aided his journey in creating the Liquid Factory. “With this new process, we were able to program robots to create the entire shoe outsole, without molds, by drawing in layers with a high-energy liquid material to create the first-ever energy-return outsole, which performs dramatically better than a typical rubber outsole,” he said in a press statement. “The all-new Liquid Factory process is also used to create a unique fit system that stretches and molds around the foot, providing a three dimensional (sic) fit.”
The outsole made using Reebok’s new technology is flexible and allows wears to “feel” the ground in a way not possible with traditional sneakers. The higher energy return means more efficiency. Runners have to exert less pressure to achieve top speed while the springy outsole is less prone to wear and tear. The wings expanding from the outsole wrap around the shoe and conform to the wearer’s foot. This adds to the comfort.
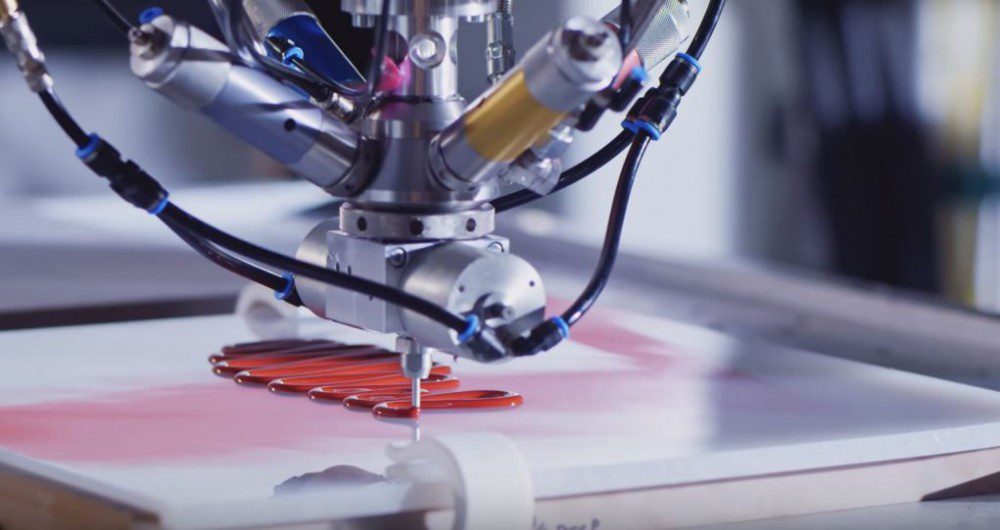
UPS AND DOWNS
While the tech at work here is impressive, it would be a lie to call them truly 3D-printed shoes. No molds are used, true, but the only part of the shoe crafted using the liquid drawing technique is the outsole and wings. The rest of the shoe- tongue, heel, etc.- are all made from the typical materials. Leather, high-quality mesh, and other fabrics are all manufactured using the same methods as other shoe companies.
However, it allows for one major change beyond the lack of molds: localized production. Almost all major shoe companies manufacture their product in Asian factories, which increases price due to shipment. Because molds are unnecessary, the Liquid Factory can be built anywhere the market demands it. Reebok originally assembled the first 3D drawn shoe in their headquarters in Canton, Massachusetts, but the factory itself has since opened in Rhode Island.
Another perk is the automation of the process. The 3D drawing is done digitally via robots. Said Chau Nguyen, Market Segment Manager for Footwear, PM North America, BASF, “the point of automation is to shorten the production cost and enable that automation. So instead of a person sitting there and putting a sole on, they were able to dispense it in 3D on the part itself— that saved a lot of time.”
HIT THE GROUND RUNNING
The first shoes using the technology were released in 2016. The Liquid Speed line was a limited production, with only 300 pairs made for the initial run. In 2018, Reebok released a Liquid Factory shoe to market- the Liquid Floatride Run. The company said the design was for “long-distance running, cardio workouts, and comfort.” It also featured the “Flexwave” material used in their previous collaboration with Modla.
The Liquid Factory is still being tinkered with and developing new innovations for future Reebok products. The latest comes in the form of 3D drawn laces, which allow for a lighter overall shoe. The price is still a bit high, compared to a simple canvas sneaker, but dropping steadily. McInnis is certainly optimistic about what the future holds for footwear. “The next generation of Liquid Factory products will be even more innovative, as we can create the entire shoe using the Liquid Factory process – outsole, cushioning and upper fit systems – the whole shoe. We are looking forward to bringing many more products to market that incorporate the ground-breaking Liquid Factory process.”
This is one factory that will never dry up, it seems.
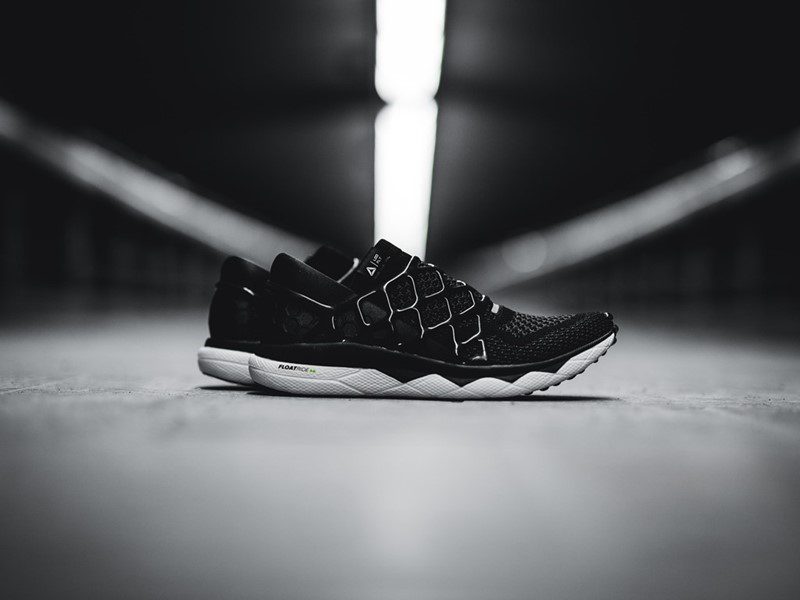
Learn more about the World of Production, and discover how vitamins, dumbbells, and game controllers are made.