As technology advances, the lifespan of electronic devices reduces. As a result, the demand for finite materials is steadily growing. At the same time, electronic waste is stockpiling in landfills. Over 80 percent of the e-waste generated ends up in landfills or incinerators. Additionally, all of the raw materials, precious metals, and rare earth elements end up in the same place.
The Fraunhofer IFF iDEAR project aims to develop an intelligent system for automated, nondestructive electronics disassembly. By combining AI, robotics, metrology, and knowledge management, the project seeks to create a certifiable, closed-loop waste management system that enhances recycling and remanufacturing efficiency. In short, the organization is developing a robot that autonomously disassembles electronics and collects reusable materials.
Revolutionizing E-Waste Disassembly
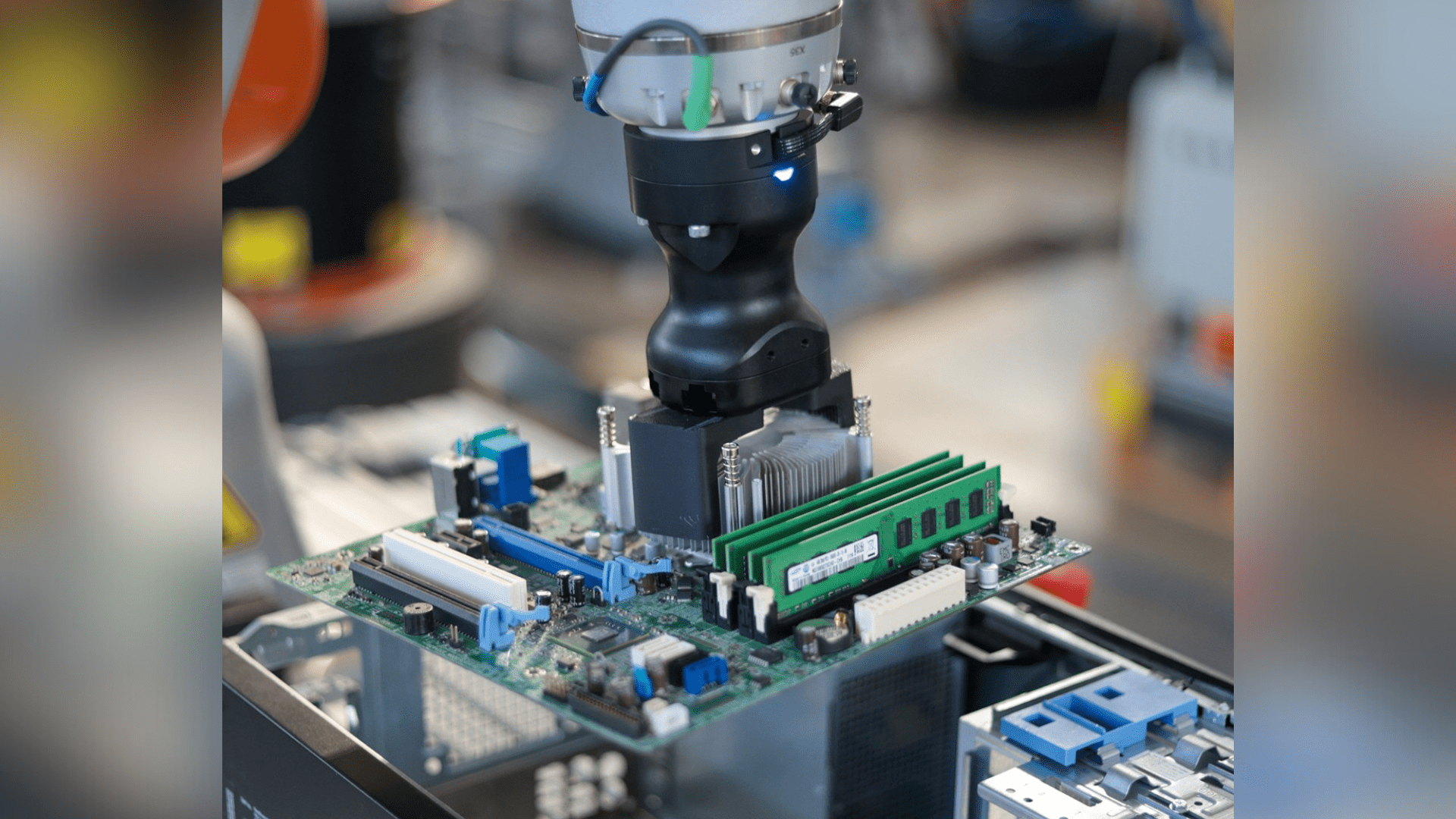
“We intend to revolutionize the disassembly of e‑waste,” said Dr. José Saenz, manager of the Assistive, Service, and Industrial Robots Group at Fraunhofer IFF. “Current solutions require substantial engineering and are limited to a particular product group.”
“In the iDEAR project, we are pursuing a data-driven methodology so that as the widest variety of products, from computers to microwaves to home appliances, can be disassembled in real-time with little engineering,”
The scientists are focusing on the disassembly of computers. However, over time, they want the system to be upgradable for any e-waste, such as a washing machine. Once the items are delivered and separated, identification and condition analysis are initiated. Then, AI-powered optical sensors and 3D cameras scan labels to identify manufacturers, product types, and components, analyze geometries and surfaces, assess fasteners like screws and rivets, and detect anomalies for efficient automated disassembly.
“Optical metrology helps scan labels and sort different parts, such as screws, for instance,” said Dr. Saenz. “Previously trained machine learning algorithms and AI interpret the image data and enable the identification and classification of materials, plastics, and components in real-time based on sensor and spectral data.” For example, the AI detects whether a screw from e-waste is concealed or rusted.
All the data are stored in a digital disassembly twin, identifying if the equipment has ever been disassembled.
Disassembly or Recovery
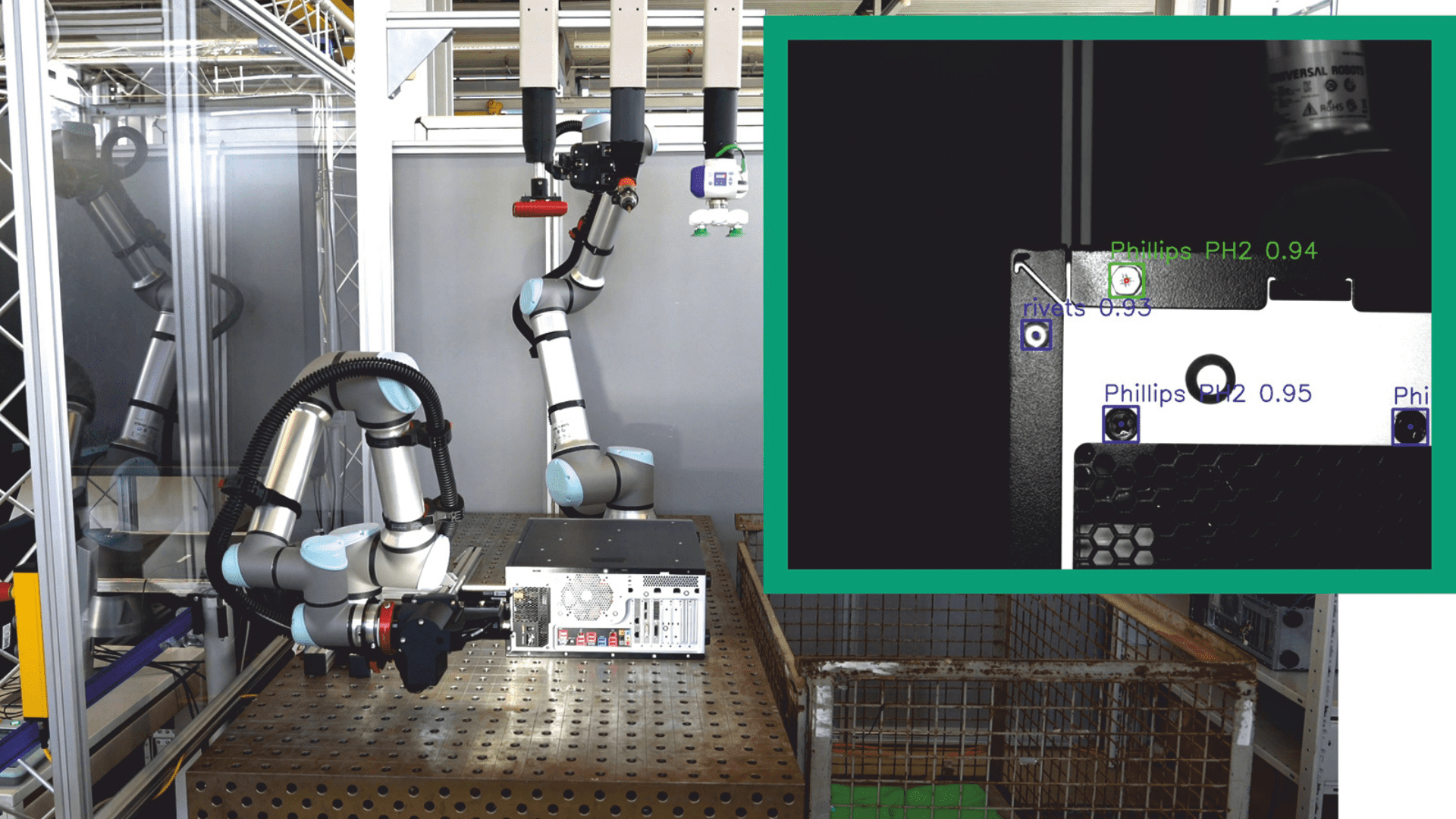
Next, the team determines whether the software should undergo complete disassembly or focus on recovering valuable components. For example, glued or mated materials hinder the disassembly process, and the same goes for rusted or deformed components. Based on this information, disassembly starts.
The robot receives instructions, such as removing pieces or opening components. Surprisingly, the demonstrator succeeded in tests to remove a motherboard from a computer, which is a very complex task that requires a high level of precision. “We used AI for that,” Dr. Saenz explained. “An AI agent is initially trained to complete the process on the simulation model, and later, we transfer the trained robot action to the real-world experimental setup.”
Several demonstrators have been developed for key subprocesses, including computer identification, digital twin integration, automated robot disassembly, and AI-driven motherboard removal. The next step is to interconnect these systems into a single integrated demonstrator capable of executing fully automated disassembly processes.
“Recycling and remanufacturing are key for manufacturing companies to ensure access to raw materials,” Saenz said. “The recovery of these materials not only reduces the environmental impact of e‑waste but also constitutes a valuable source of raw materials for new products.”