The National Low Income Housing Coalition stated that the world has grown to a need for more than 7 million homes to address the affordable housing crisis. Concrete 3D printing is being proposed as a possible solution to this problem.
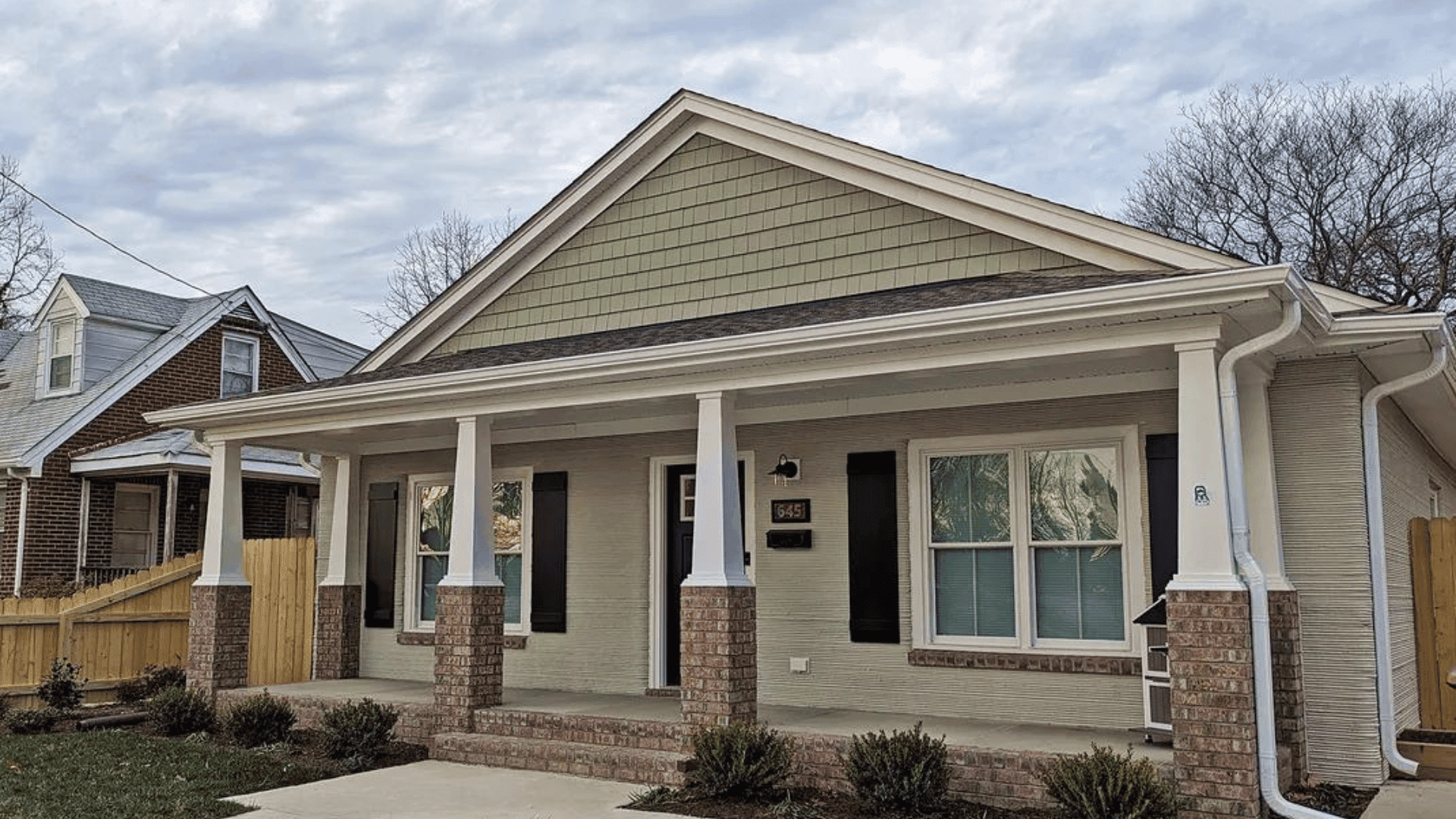
Habitat for Humanity Peninsula and Greater Williamsburg chapter is working to build 3D printed houses, including one recent build that was 1,300 square feet and only took 40 hours to build. Janet Green, the chapter’s chief executive officer, says each home has been less expensive than the previous.
The recent build cost Habitat for Humanity approximately $215,000, which amounted to $25,000 less than the first one they constructed, and the land was free from the city’s housing authority.
“We suspect the eventual cost to print future 3D homes for Habitat would be around $180,000 to $190,000,” she says. The average listing price for a home that size in the area of construction is over $260,000.
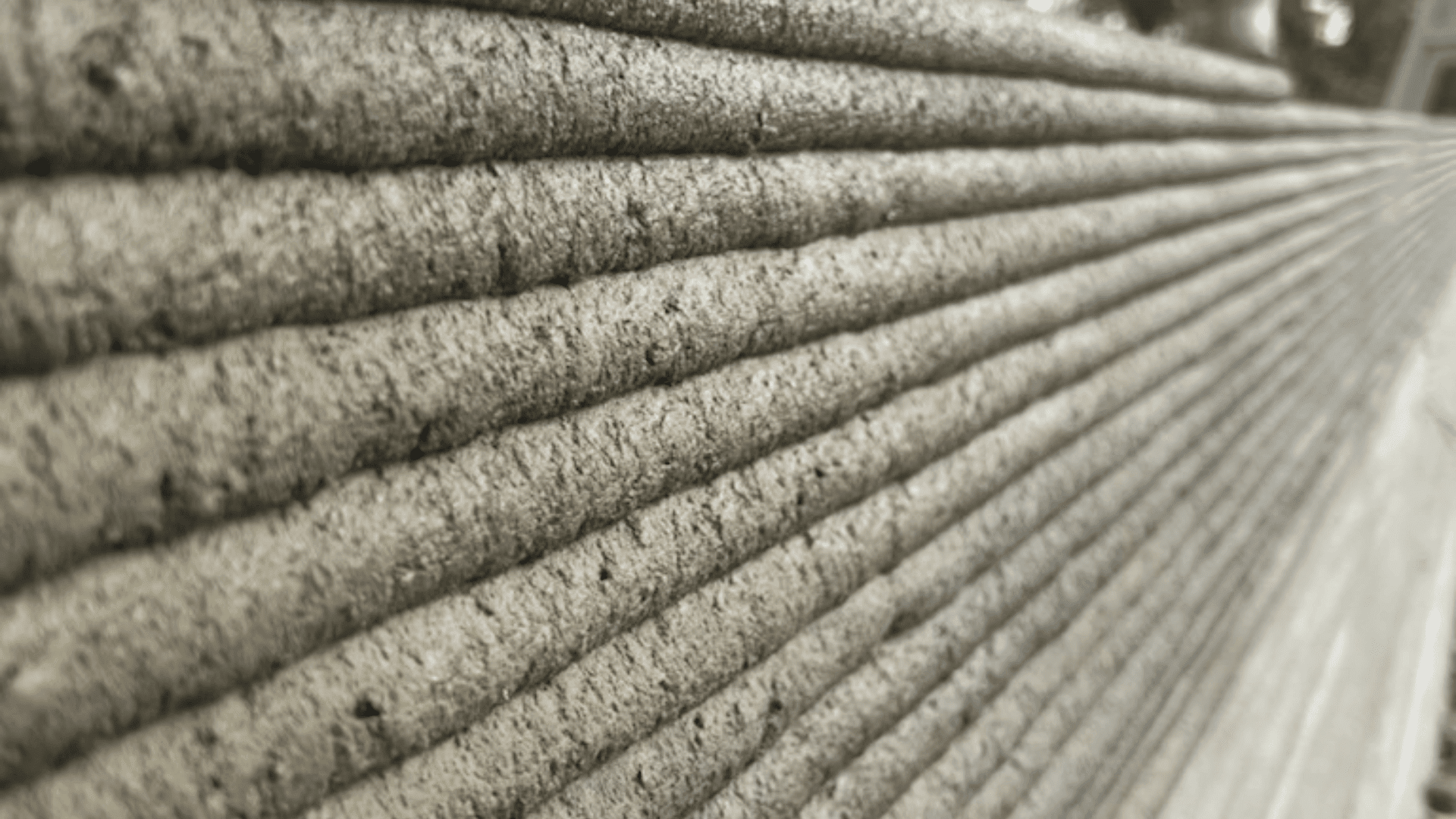
Apart from speed and affordability, construction of 3D-printed houses has shown to be cleaner, resulting in less waste. The United States creates 600 million tons of construction and demolition debris annually. Companies like Homes by Creation are pioneering the use of 3D-printed concrete to build cost-effective, sustainable homes, offering a potential solution to the affordable housing crisis.
3D-printed homes are also better insulated, which makes them more energy efficient and lowers heating and cooling costs. They also require less labor and can be built with only one or two people, which is beneficial at a time when there is a shortage of construction workers.
The company that printed the three Habitat houses, Alquist 3D, moved its headquarters from Iowa to Greeley, Colorado, last year. There, they plan to build 100 homes as part of a 300-home Habitat for Humanity project
In addition to building houses, they are also working with Aims Community College to create a 3D-printing curriculum, which will help train the workers who are needed to grow this industry.
Explore Tomorrow's World from your inbox
Get the latest science, technology, and sustainability content delivered to your inbox.
I understand that by providing my email address, I agree to receive emails from Tomorrow's World Today. I understand that I may opt out of receiving such communications at any time.
In addition to Alquist 3D, Texas-based Icon is working with Lennar, the second-largest home builder in the US, to print 100 houses in a 500-unit development. The median comparably sized Austin-area home lists for over $800,000, but these units are currently priced between $469,990 and $578,990.
The exterior and interior walls for each of the printed homes were completed in two weeks and the traditional finishing in approximately six months.
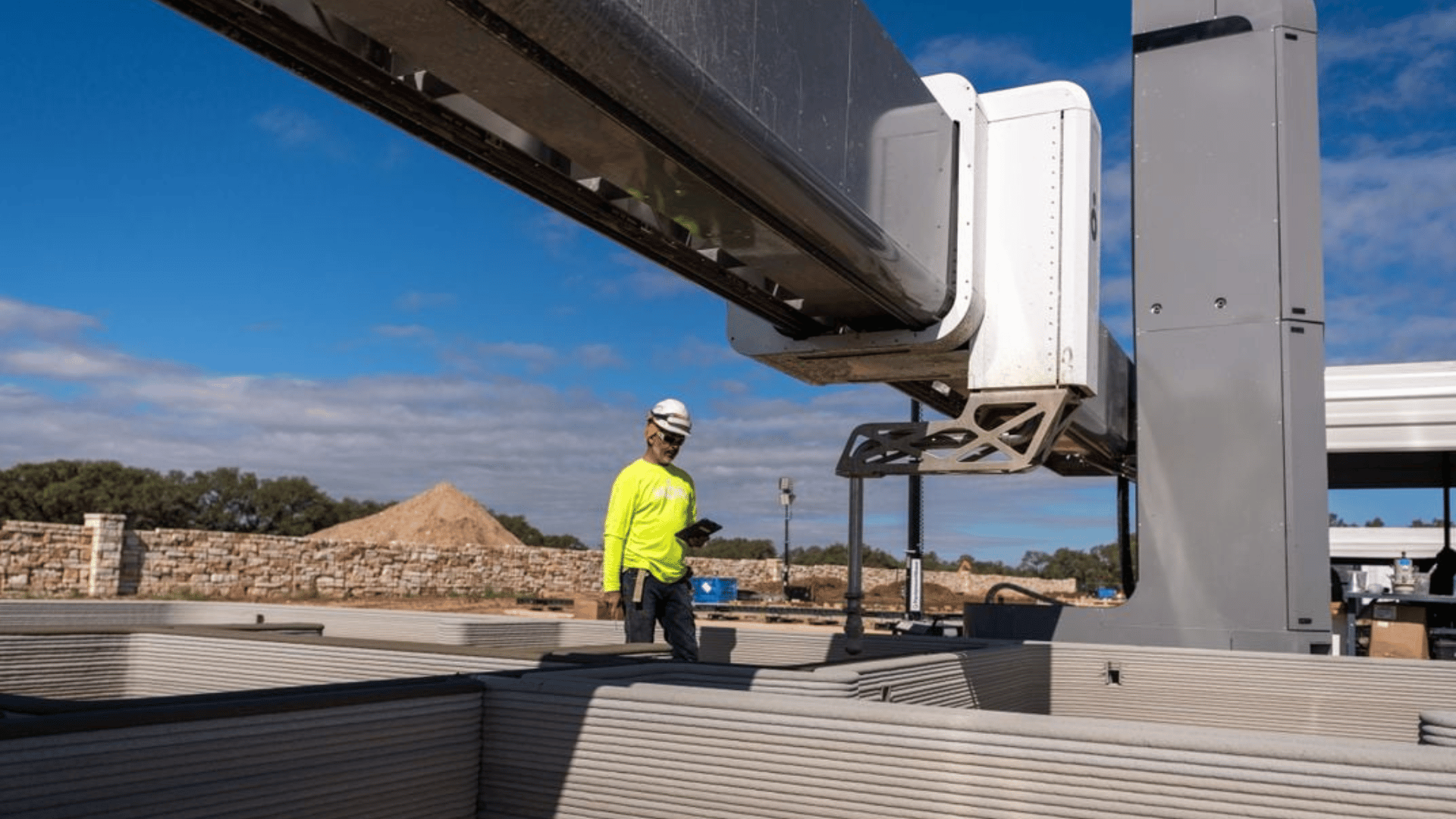
“We’re introducing drastic time saving, which of course translates into a huge value add in terms of costs and financing,” says Melodie Yashar, Icon’s vice president for building performance and design.
In partnership with New Story, a San Francisco nonprofit building housing in Latin America, Icon also printed a community of homes that were granted to people in extreme poverty in Mexico. The company has also printed military barracks and is working on a $57 million contract with NASA to work on moon habitats.
“What if we could build houses that work twice as good, in half the time and at half the price?” Jason Ballard, Icon’s CEO, asked at a conference in 2022. “What kind of problems could we solve? And what kind of opportunities would open up before us?”