Researchers at Northwestern University found a new, simpler way to break down plastic waste. According to the researchers, they used a non-toxic, environmentally friendly, solvent-free process first using an inexpensive catalyst to break down the most common plastic in the polyester family. Then, they converted it to monomers, building blocks for plastics. They envision the monomers could be recycled into new polyethylene terephthalate (PET) products or valuable materials.
Plastic Recycling
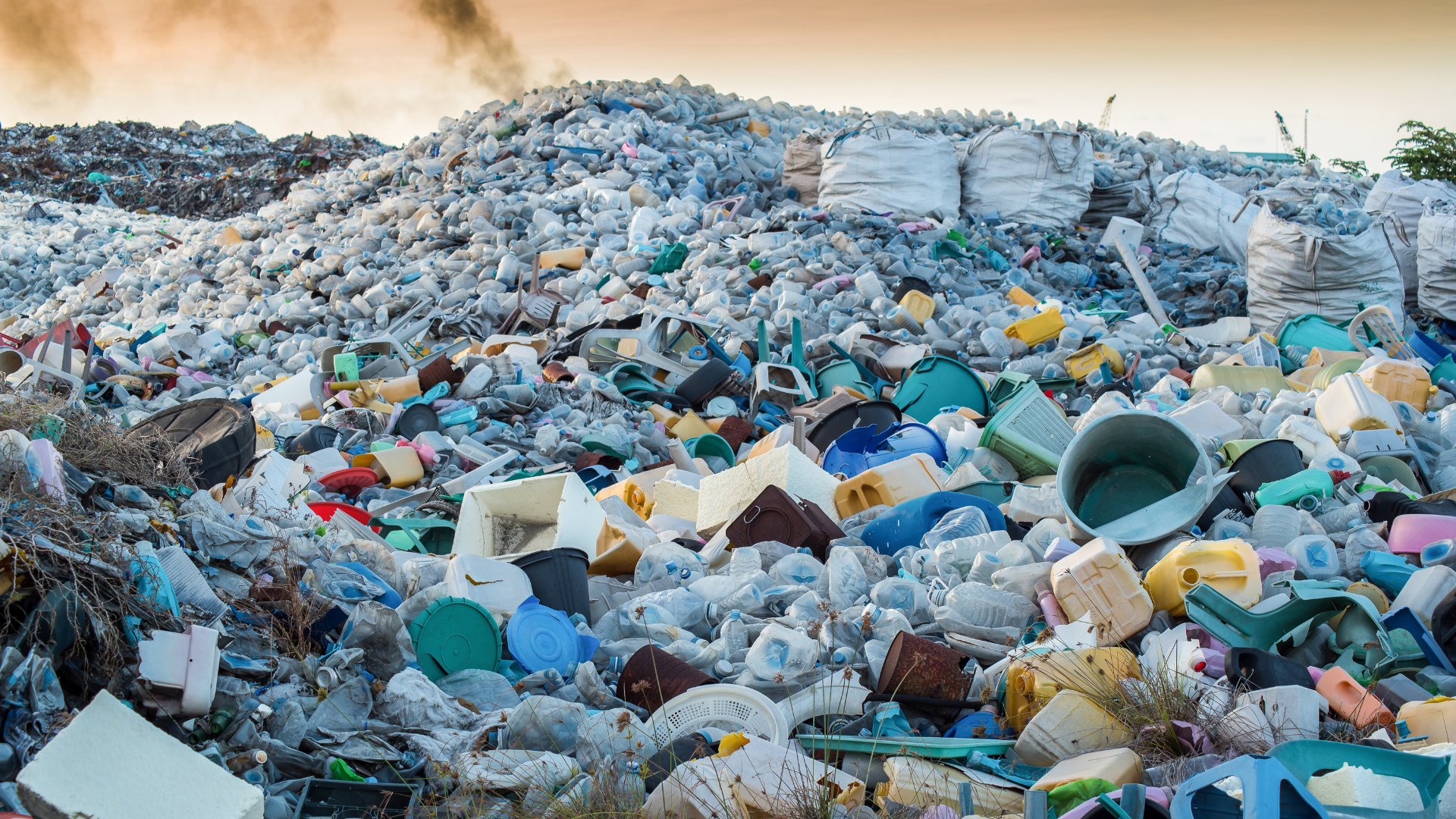
“Our study offers a sustainable and efficient solution to one of the world’s most pressing environmental challenges: plastic waste,” said Naveen Malik, the study’s first author. “Unlike traditional recycling methods, which often produce harmful byproducts like waste salts and require significant energy or chemical inputs, our approach uses a solvent-free process that relies on trace moisture from ambient air.”
He continued, “This makes it not only environmentally friendly but also highly practical for real-world applications.”
To conduct the new study, the researchers used a molybdenum catalyst and activated carbon—both of which are inexpensive, abundant, and non-toxic materials, according to the press release. To initiate the process, the researchers added PET to the catalyst and activated carbon and then heated up the mixture. Polyester plastics are large molecules with repeating units linked together with chemical bonds.
After a short period of time, the chemical bonds within the plastic broke apart.
Next, the researchers exposed the material to air. With the tiny bit of moisture from the air, the material turned into terephthalic acid (TPA) — the highly valuable precursor to polyesters. The only byproduct was acetaldehyde, a valuable, easy-to-remove industrial chemical.
“Air contains a significant amount of moisture, making it a readily available and sustainable resource for chemical reactions,” Malik said. “On average, even in relatively dry conditions, the atmosphere holds about 10,000 to 15,000 cubic kilometers of water. Leveraging air moisture allows us to eliminate bulk solvents, reduce energy input, and avoid the use of aggressive chemicals, making the process cleaner and more environmentally friendly.”
The Advantages
The researchers’ press release states that the process is “fast and effective.” It says, “In just four hours, 94 percent of the possible TPA was recovered. ” The catalyst is reportedly “durable and recyclable,” with the ability to be used time and time again. “The method works with mixed plastics, selectively recycling only polyesters. With its selective nature, the process bypasses the need to sort the plastics before applying the catalyst — a major economic advantage for the recycling industry.”
They also tested the process on common materials such as plastic bottles, shirts, and mixed plastic waste, which also proved to be effective. It even turned colored plastic into colorless TPA.
Their next step is trying to scale it for industrial use.
“Our technology has the potential to significantly reduce plastic pollution, lower the environmental footprint of plastics, and contribute to a circular economy where materials are reused rather than discarded,” Malik said.