Inspired by how spiders create intricate silk structures, researchers at the Institute of Technology University of Tartu in Estonia have created a new type of self-building robot that can “spin” new physical components instantly using a special kind of heated polymer.
Self-Building Robots
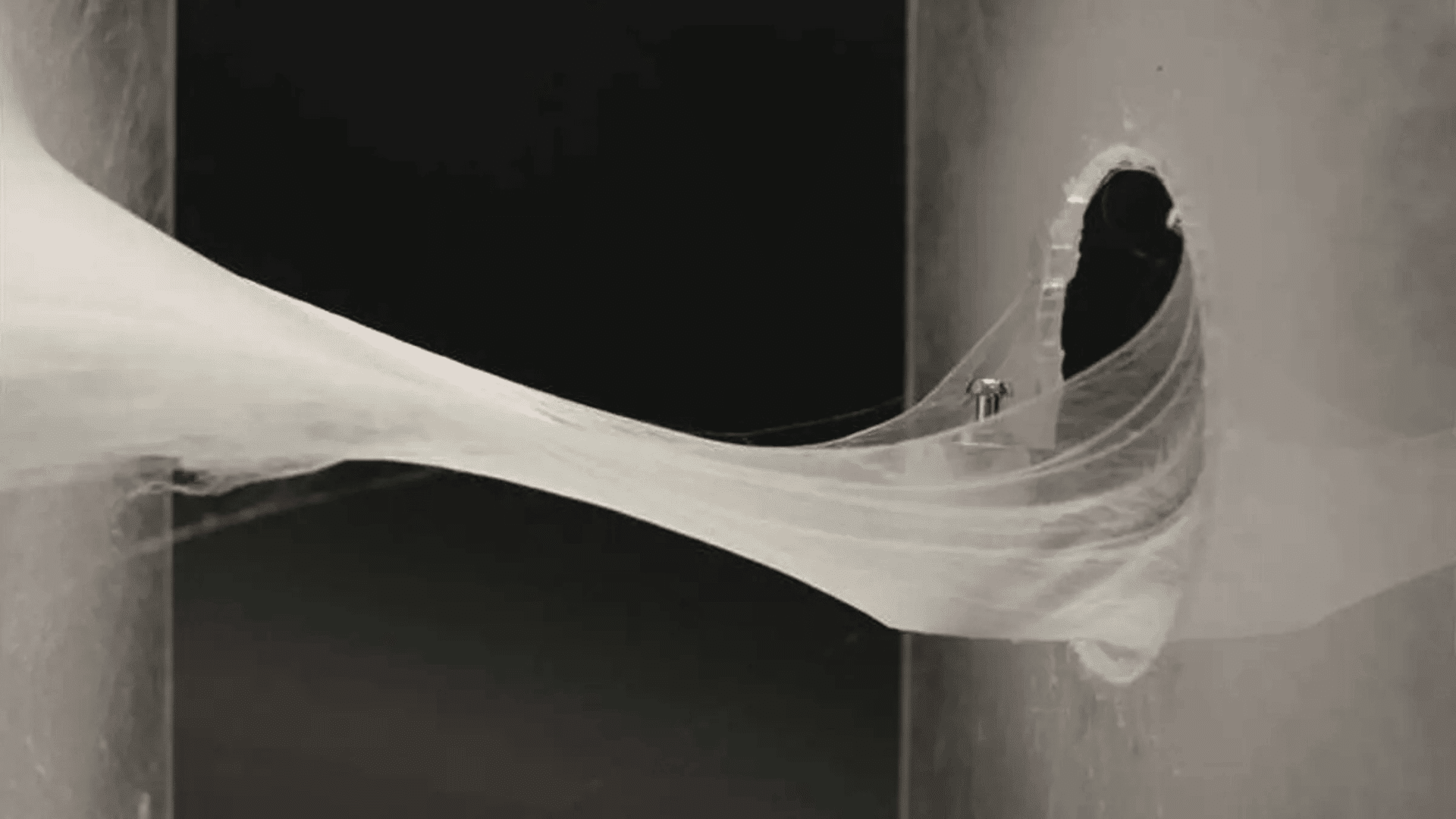
Most robots contain fixed components, which are typically built in factories and optimized for specific tasks. The downside of this type of design is that the components lack versatility.
The new type of robot alters the landscape by allowing robots to build their own components on demand as needed. The polymer used to build new components is carried in a liquid form, extruded through a heated nozzle, and quickly cools into solid fibers.
The robot’s heated polymer strands mimic spider silk spinning techniques and can adhere to a variety of surfaces. The team reports that the robot can rapidly spin fibers into custom-made structures created for a specific task or environment.
Testing the Technology
One test that the researchers conducted was to have the robot build a bridge across a gap. The robot spun fibers across a simulated disaster area to form a bridge strong enough to enable a small car toy to cross.
A second test involved tasking the robot to make tools, such as a delicate gripping limb that picked up a flower without damaging it. These types of tools could tackle tasks that pre-built robotic grippers may damage.
In a final test reminiscent of Spider-Man, the robot was tasked with anchoring itself to various surfaces. Researchers tested whether it could adhere to non-sticky surfaces such as oily sponges, waxy leaves, and slippery Teflon.
One potential use for this type of technology in the future is disaster relief, as the robots could quickly and efficiently spin bridges and safe pathways through hazardous debris. It may also be useful in the construction industry, as it could build dynamic temporary structures on-site, reduce the need for pre-made components, and allow more adaptive infrastructure.
“Our approach takes a cue from spiders as nature’s ingenious engineers, yet we found a loophole that lets us sidestep the limitations and excessive complexity of directly imitating spiders,” said Marie Vihmar, lead author of the study.