Caterpillar announced the successful testing of a 600-volt battery-powered powertrain, showing off its performance, reliability, and durability. According to the equipment manufacturer, the tests prove that its factors compare to those of a conventional 74-horsepower diesel engine while reducing maintenance and operating with zero tailpipe emissions.
Electric Field Elevator
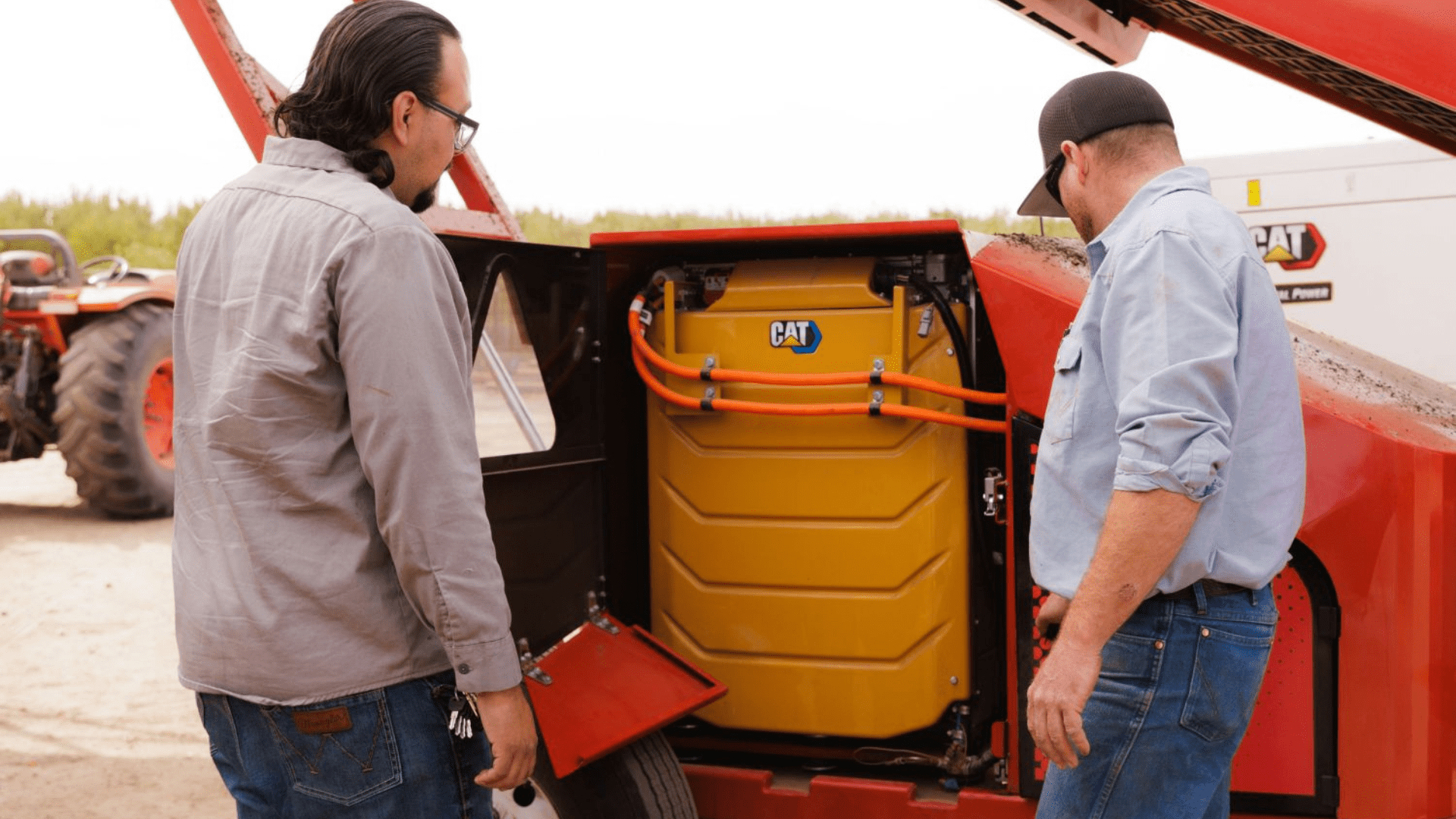
The tests occurred during the fall harvest season in the Central Valley region of California, specifically the almond and walnut orchards in the Golden State. One site was Heinrich Farms, a 1,200-acre crop farm in Modesto. This is significant because the electric powertrain is for a battery-powered field elevator for nut-harvesting. In collaboration with Flory Industries, a big name in the production of nut-harvesting equipment, the unit operated an entire 10-hour workday on a single charge.
“The electrified field elevator from Flory was reliable and unloaded our harvest as fast as conventional equipment powered by diesel engines while generating far less noise,” said Jerad Heinrich, Orchard Manager for Heinrich Farms. “It lasted an entire day of work without stopping for a recharge, and we’re eager to use it again for our next harvest as the technology continues to progress.”
Field elevators are key pieces of equipment for harvesting tree nuts. The equipment transfers the nuts into reserves, processing an incredible 50,000 to 250,000 pounds of nuts daily during peak fall harvest season. They’re typically powered by diesel engines and operate at low idle between loads for about 80% of the time, accounting for about 45% of their total fuel consumption. Due to the long periods of sitting unused combined with the need for immediate power, field elevators are an ideal candidate for electrification.
Sustainable Future
Caterpillar says replacing the diesel engine with an electrified powertrain could eliminate up to 126 pounds of carbon emissions per machine daily. Additionally, the switch could reduce fuel, transportation, and storage costs.
Furthermore, the battery-powered field elevator is designed to link with Cat Connect, Caterpillar’s digital technology suite that enables users to monitor the equipment remotely during operation and charging periods.
“We’ve gained valuable insights from working with Flory to apply our knowledge of electrification and high-voltage systems to the challenging environments of working California farms,” said Steve Ferguson, Senior Vice President of Caterpillar Industrial Power Systems.