KEEL Labs™ founders Tessa Callaghan and Aleks Gosiewski went from design students to designing the Kelsun™ fibre. This fibre is made from a seaweed biopolymer called alginate, which can seamlessly integrate into existing yarn and textile infrastructure to lower the carbon footprint of clothing production.
With a background in design and innovation, Tessa leads the global expansion and adoption of Keel Labs’ flagship product while working across the value chain to align partners, brands, and manufacturers to achieve their sustainability goals. As a Forbes 30 Under 30 member, Tessa is a thought leader in her space, bridging disparate fields to create innovative solutions at a global scale.
We had the opportunity to speak with Tessa about her beginnings in sustainable fashion, how Kelsun™ fibre went from idea to reality, and the fashion industry’s future.
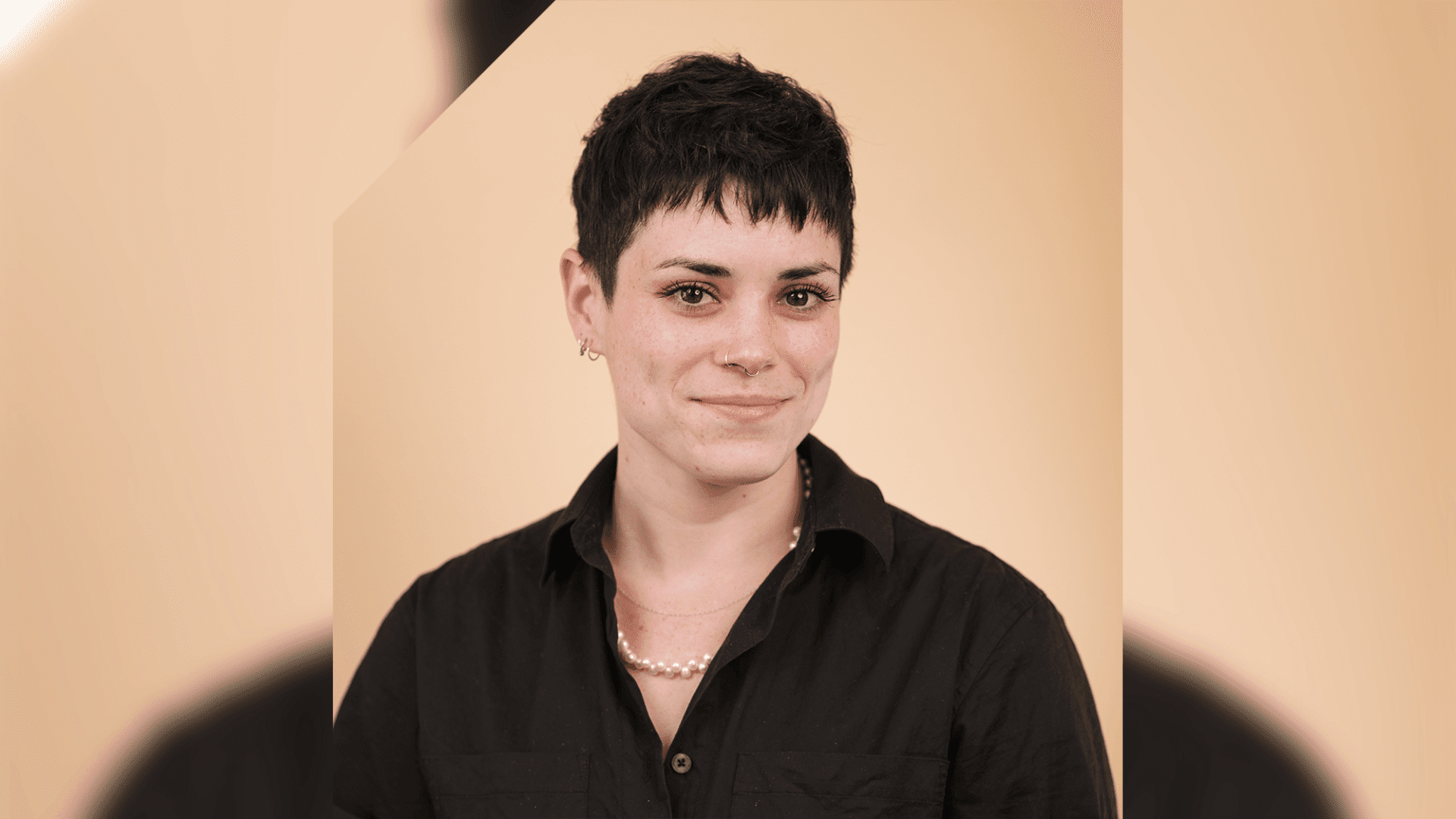
Tomorrow’s World Today (TWT): What originally inspired you to go into the field of sustainable fashion?
Tessa Callaghan (TC): It is challenging to work in the fashion industry and not face the realities of waste and pollution firsthand. Fundamentally, a designer’s job is to solve a problem, however seemingly big or small. While myself and my co-founder Aleksandra began working in the industry, it quickly became clear that there weren’t any available solutions to solve for the negative impacts garment production created as well as the ongoing challenge of making garments with the feel, function, and fit they require. The only clear path to resolving this discrepancy was to dive into the design of materials that have the ability to address the inherent needs of what is now our customer: the textile industry as a whole.
TWT: How did the design of Kelsun™ fibre come about? How did it go from idea to reality?
TC: We set out to explore what a solution would need to look like to mitigate the planetary harm created by the fashion industry as a whole, from waste accumulation to soil degradation to fresh water usage and beyond. What we realized was that in starting from the fundamental building blocks of textiles, fibers, the major drivers of impact could be tailored and modified for the better. Further, we knew that time was of the essence, meaning we have to work with and not against existing supply chains and ensure raw material resources are abundantly available today. By defining specific parameters, we quickly eliminated land-based agriculture and toxic chemicals from the equation, leaving us only with the ocean to search for raw materials that were renewable and readily available. Enter: seaweed, one of the most rapidly growing and regenerative organisms on the planet. By working with alginate, a known biopolymer source found in seaweed, and designing with existing manufacturing systems in mind, we were able to prove that yes it would be possible to supply better, more fundamentally sustainable products to an industry in dire need. From there and with the growing demand from brands and support of forward-thinking investors, we were able to develop and scale our product, Kelsun, a fiber that eliminates the need for arable land and petrochemicals, all while promoting a cleaner, more prosperous planet.
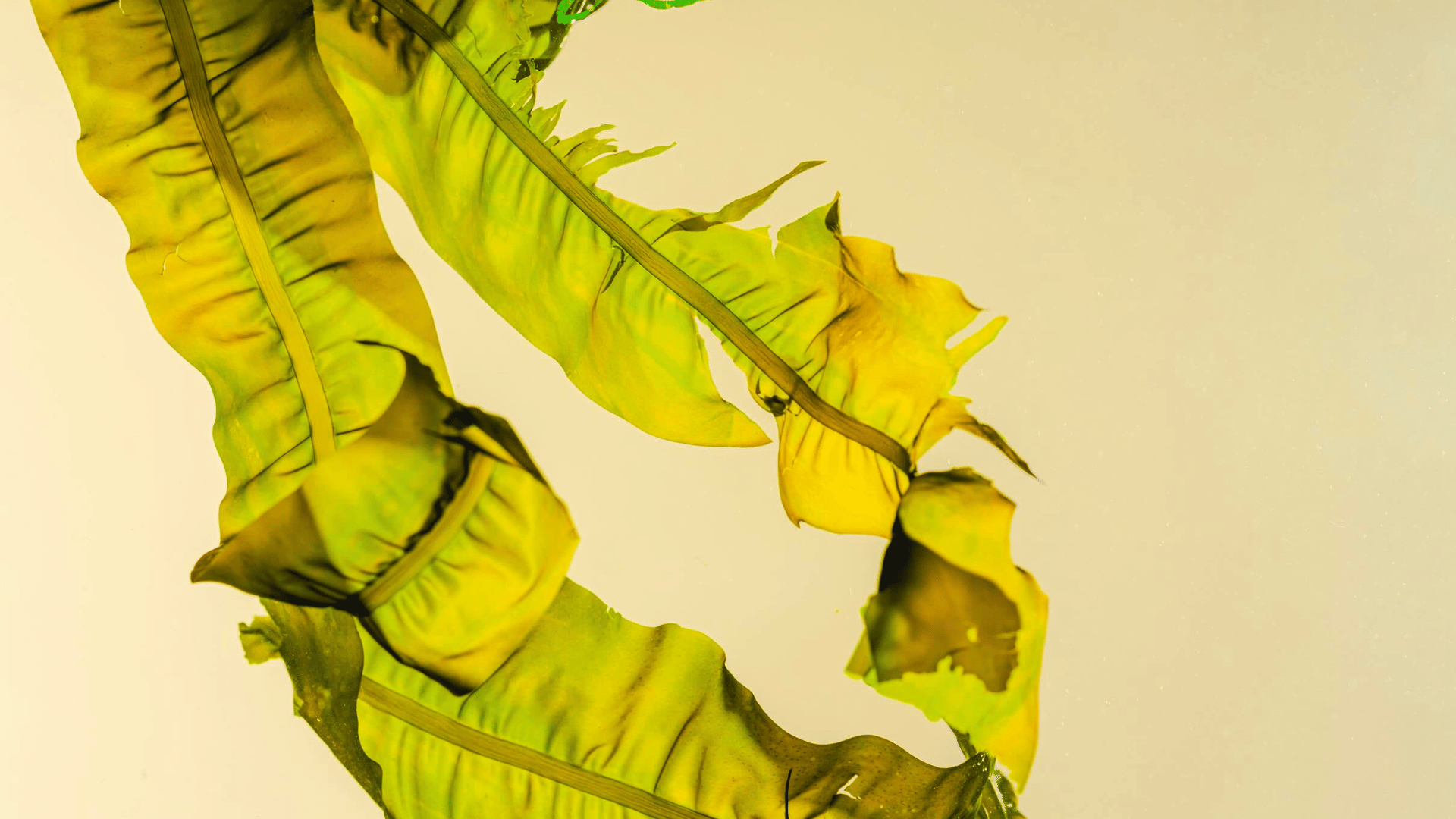
TWT: How does a piece made with Kelsun™ fibre compare to traditional textiles in terms of environmental impact?
TC: Kelsun was created to tackle the plethora of negative impacts associated with traditional textiles. Because we source our raw materials from the ocean, Kelsun reduces the reliance on water, soil, and pesticides associated with the growth of conventional fibers. Additionally, our products do not contain petrochemicals, making them safer for workers throughout production, and for the end consumer wearing them. The result is a biodegradable, certified non-ecotoxic* textile solution that is designed to leave no harmful trace at any point of its life.
(*In accordance with DINSPEC #4872)
TWT: Walk us through the design process behind a piece made with Kelsun™fibre fabric. How is a piece designed, how is it produced, etc.?
TC: We developed Kelsun to fit directly into the industry’s day-to-day functionality and facilitate the ongoing creativity of brands and their design teams. Each company works a bit differently, though the overall process is quite straightforward. After being inspired by a fabric or garment sample made with Kelsun fibers, teams will design and spec their target product. From there, they will send their specified parameters to their mills who will turn Kelsun fibers into yarns, knit or weave them into textiles, and cut and sew them (often with dyeing and printing) into end garments.
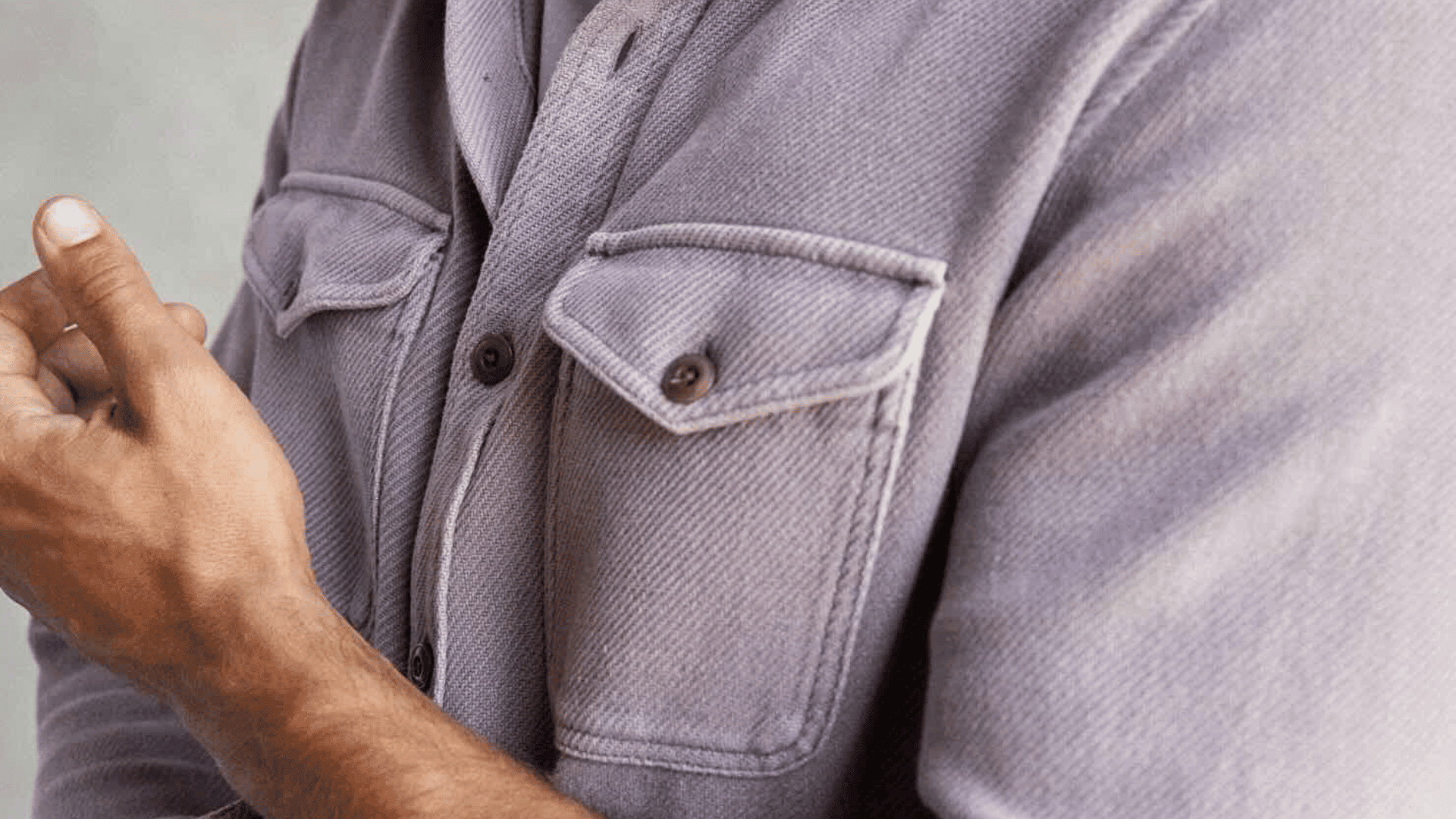
TWT: Did you face any challenges in the design process? If so, how did you overcome them?
TC: There is a reason that so few solutions exist today in the next-generation materials space, it is certainly a challenge and we have faced many. At first, our biggest hurdle was overcoming the technical challenges of creating a fiber that performed to the strength, durability, and nuanced hand feels required by apparel and functional textile products. This took time and a well-tailored team of dedicated experts to study, test, and develop our technology. The second biggest challenge, and what we face now, is aligning timing and resources across the supply chain. This requires simultaneous buy-in not just from brands, but also from their suppliers and mills, all of which is underlined by the demands of the end customer, or consumer. As such, we work diligently to ensure every relationship we build is aligned toward the same end goal and that we are able to provide resources to continue to educate and collaborate at all points.
TWT: In addition to Kelsun™ fibre being more environmentally friendly than traditional textiles, what other sustainability practices or initiatives does Keel Labs™ participate in?
TC: Prioritizing people and the planet is paramount to us. We uphold that core value in a number of ways, whether that’s volunteering with local non-profits or up-fitting our office with second-hand materials and furniture. We also love collaborating with companies that align with us and are pushing boundaries in innovation, like our partnership with design firm Interesting Times Gang, who utilized Kelsun in the upholstery of their ‘Kelp Chair’, made completely from materials derived from seaweed.
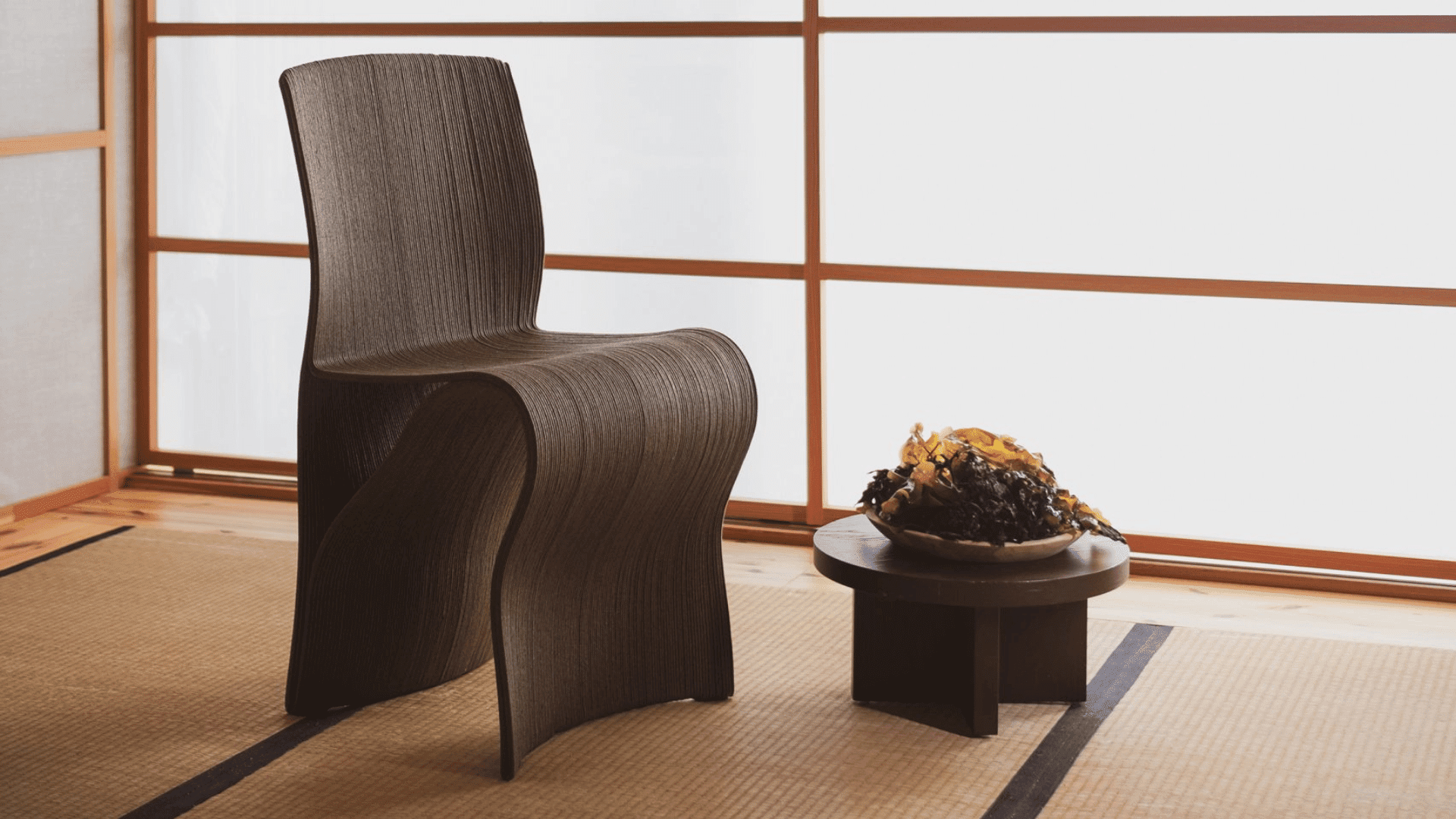
TWT: What is your favorite piece you’ve designed and why?
TC: Every new piece made with Kelsun is our favorite. It is our goal to provide products that serve a diverse set of applications, which means its less about one specific product, and more about expanding the use cases we work within. This means that every time a new product or piece is developed, it furthers our core mission of providing better performing and more holistically sustainable products available to all.
TWT: KEEL Labs™ has previously partnered with designers such as Stella McCartney and MR. BAILEY. Tell us about the pieces you created with these designers. What was the most rewarding part of these collaborations?
TC: When working with designers, we support their vision by giving them creative reigns and work collaboratively to support bringing our shared goals to reality.
Stella McCartney debuted the first Kelsun dress on the runway at her Summer ’24 show. Partnering with Stella for our runway debut was groundbreaking, especially as it showcased an entirely new construction and garment application that we wouldn’t have considered without their creative interpretation of our materials. Stella is known for being a pioneer for sustainability in luxury fashion, phasing out virgin leather and fur, as well as incorporating next-generation materials throughout her line.
Working with Mr. Bailey was an incredible experience and resulted in a truly innovative piece that reflects our shared vision, mission, and passions. His biophilic approach to design was inspiring to witness and knew that with it he would create something entirely unique. He chose to use Kelsun in multiple forms: as the fabric for the outside of the vest, and Kelsun in its fiber form as a filling to add structure to the garment. This kind of thinking is exactly what we look for in a partner, and helps us steer the future of Kelsun.
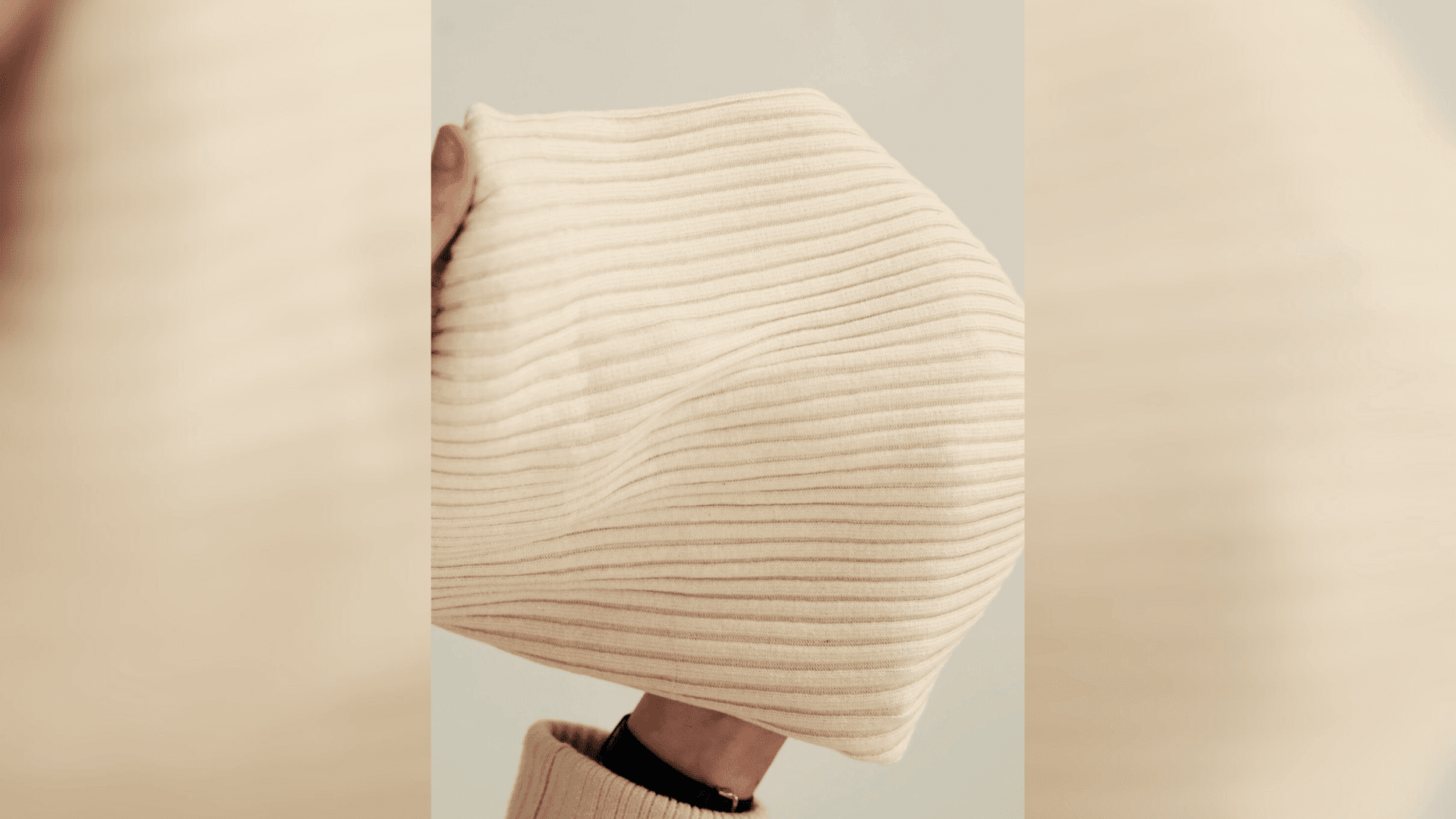
TWT: What is your favorite part of working for Keel Labs™?
TC: There are so many joys that come with building Keel Labs and bringing Kelsun into the world. One of the most exciting is witnessing the brands we work with apply the design development process we sought to enable in the foundation of the company, bringing their products to life in a way that reflects both impact and functionality standards demanded by the industry as a whole. When working with fibers, it can be challenging to imagine the end result. Seeing final products come to life in a way that is tangible and accessible is by far the most inspiring piece of the puzzle.
TWT: What are some of your goals for the future of Keel Labs™?
TC: We are extremely eager about the future of Keel Labs in all the facets of our work from scale to technology developments to wide-spread implementation. One of the upcoming goals we are most looking forward to is the various retail launches we have planned with our brand partners. Having Kelsun available for global consumers to interact with and add to their wardrobes and daily lives is why we began. Though there is much more hard work ahead of us, seeing our ideas come to fruition continues to drive our teams forward and motivate us throughout our journey.